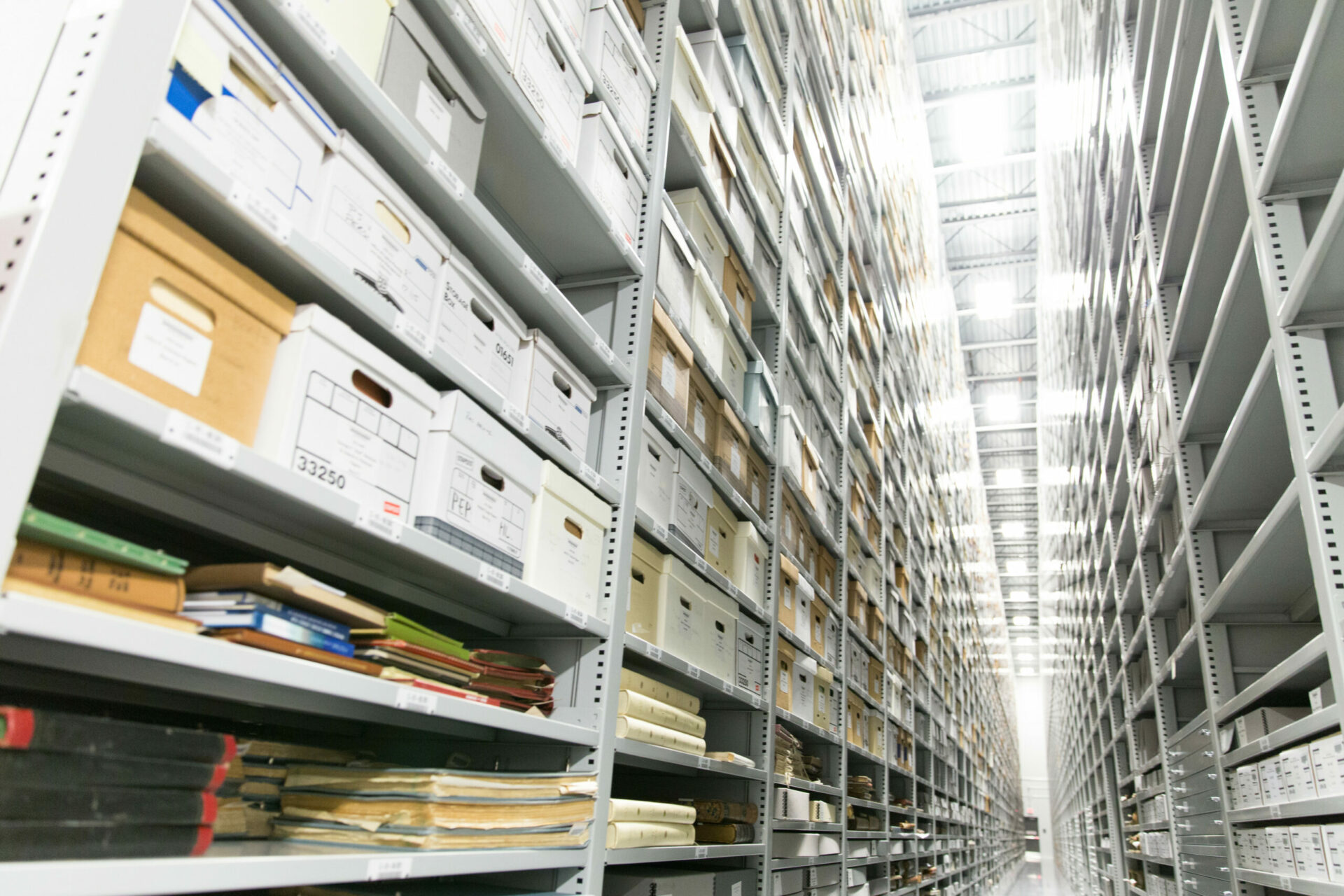
Introduction
Industrial/Warehouse storage is important for public safety as it ensures proper organization of materials and equipment, reducing the risk of accidents and injuries. It also allows for efficient emergency response by enabling easy access to safety equipment and clear evacuation routes in case of emergencies.
Employers and warehouse managers have a responsibility to create a safe work environment for their workers, minimizing the risk of injuries, fatalities, and the potential for hazardous incidents. Designing a safe warehouse environment involves understanding the key facts about warehouse injuries and fatalities, recognizing the challenges posed by today’s warehouse operations, exploring warehouse safety standards, and implementing effective safety practices. In this blog, we will delve into the various aspects of designing and managing a safe warehouse environment, including the role of industrial storage, the impact of the e-commerce boom, essential safety standards, training workers in safety procedures, and implementing an emergency response plan.
Understanding Warehouse Safety
As the hub of industrial activities, warehouses pose unique safety challenges that must be addressed. Warehouse safety encompasses a range of practices designed to protect workers, material handling equipment, and the facility. Understanding warehouse safety begins with recognizing the key facts about warehouse injuries and fatalities, as well as the crucial role that industrial storage plays in ensuring workplace safety.
Key Facts about Warehouse Injuries and Fatalities
Warehouse injuries can have serious consequences, leading to significant productivity loss and, in some cases, fatalities. Musculoskeletal disorders, caused by manual handling, lifting heavy items, and repetitive motions, are common among warehouse workers. Implementing emergency response plans is crucial for addressing warehouse hazards, such as fires, chemical spills, and accidents involving material handling equipment. Additionally, warehouse environment noise levels can impact worker safety, while warehouse fire safety protocols are essential for preventing fatalities.
Industrial storage solutions play a critical role in promoting workplace safety in warehouses. Storage equipment, such as racks, shelving, and pallet racking systems, should be ergonomically designed to ensure worker safety during the handling of materials. The design of storage solutions must cater to the specific needs of the warehouse, maximizing storage capacity while maintaining safety standards. Proper warehouse storage design also encompasses the safe storage of hazardous materials, minimizing the risk of workplace injuries. By ensuring the efficient and safe storage of items, industrial storage solutions contribute to a safe work environment for warehouse workers.
Recognizing Today’s Warehouse Safety Challenges
Maintaining a secure working environment is a challenge. The e-commerce boom has brought about significant changes in warehouse operations, impacting overall safety. Managing constant workflow and workload changes is also crucial due to the unseen hazards they pose. It’s essential to recognize these challenges to ensure the implementation of effective safety measures and the reduction of workplace incidents. Understanding the impact of these challenges on warehouse safety is vital for the well-being of workers and the overall efficiency of operations.
The rise of e-commerce has revolutionized the way warehouses operate, presenting both opportunities and challenges for warehouse safety. With the increasing demand for online orders, warehouse workers face a higher workload and productivity expectations to meet customer demands. The integration of warehouse robotics and automation can improve efficiency but also requires careful consideration of worker safety practices. Furthermore, the increased traffic within the warehouse poses safety risks for pedestrians, emphasizing the need for proper safety measures. Warehouse loading docks, which handle heavy items, must also be equipped with the necessary safety protocols to prevent accidents. Warehouse clearances and storage space needs are also impacted by the online ordering trends, thereby necessitating a careful assessment of safety standards in these areas of warehouse operations.
Constant workflow and workload changes can introduce unseen hazards in the warehouse environment. Warehouse workers must adapt to changing work demands, which requires regular training and awareness of specific hazards associated with workload shifts. Warehouse safety standards should address the implications of workload fluctuations, ensuring workers’ safety during high-demand periods. In addition, warehouse workers must be trained in handling heavy items safely, reducing the risk of musculoskeletal injuries. Hazardous chemicals are also commonly present in warehouse operations, requiring workers to be educated on the safety practices for handling them. By recognizing the challenges posed by constant workflow and workload changes, employers can implement the necessary measures to protect their workers and maintain a safe work environment.
Exploring Warehouse Safety Standards
To ensure the safety of warehouse workers, it is essential to explore the warehouse safety standards set forth by regulatory authorities, such as the Occupational Safety and Health Administration (OSHA). Warehouse safety standards encompass guidelines for material handling, storage equipment, fire protection, and other critical areas of warehouse operations. Adhering to these standards helps minimize the risk of workplace injuries and fatalities. Warehouse safety standards also emphasize the importance of personal protective equipment (PPE) and regular safety training. In the following sections, we will delve into the specific aspects of warehouse safety standards and best practices for designing a safe warehouse environment.
Pallet racking is a common storage solution in warehouses, providing efficient storage for palletized goods. Adhering to best practices for pallet racking ensures the safety of workers and the integrity of stored items. Here are some best practices for pallet racking:
- Proper installation: Ensure pallet racking is installed correctly, following manufacturer guidelines and safety standards.
- Regular inspections: Regularly inspect pallet racking for signs of damage, such as bent or damaged beams, and promptly address any issues.
- Load capacity: Adhere to load capacity limits, distributing the weight evenly on each shelf to maintain stability.
- Fall protection: Install appropriate measures, such as safety netting or backstops, to prevent items from falling off racks.
- Worker training: Train workers on safe loading and unloading procedures, including proper forklift operation and securing of pallets.
- Following these best practices for pallet racking helps create a safe working environment, reducing the risk of accidents and damage to stored items.
Creating a Safe Warehouse Design
It is all about creating clear pathways for workers and machinery, minimizing the risk of collisions and injuries. It also considers the safe storage of hazardous materials, segregating them from other items to prevent accidents. Additionally, warehouse design must minimize the risk of worker injury by ensuring the proper positioning of equipment, reducing the likelihood of strains, falls, or other accidents. Warehouse safety standards should inform the design of storage solutions, ensuring that racks, shelving, and other equipment are ergonomically designed for easy access and safe handling of materials. By considering safety standards in the warehouse design process, employers can promote a safe work environment for their employees.
Well-designed storage solutions optimize space, improve workflow, and minimize the risk of workplace injuries. Industrial storage equipment, such as storage racks, shelving systems, and pallet racking, must be constructed with safety in mind, providing stable and secure storage for materials. By maximizing the use of warehouse space, efficient storage equipment reduces the likelihood of accidents caused by overcrowded or disorganized storage areas. Furthermore, high-quality storage equipment ensures the safe and secure storage of materials, preventing hazards such as falling objects and collapses. By investing in effective storage equipment, employers can enhance workplace safety and improve warehouse efficiency.
Proper warehouse design plays a crucial role in hazard prevention and worker safety. Thoughtful warehouse design minimizes the risk of workplace injuries, creating a safe work environment for employees. By addressing common warehouse hazards through design, the chances of accidents and injuries can be significantly reduced. Some ways to avoid common warehouse hazards through design include:
- Clear pathways: Ensure clear walkways are present for workers to move safely through the warehouse.
- Adequate lighting: Proper illumination improves visibility, preventing trips, and falls.
- Fire safety measures: Designate fire exits, install fire extinguishers, and ensure clear paths for emergency evacuation.
- Properly marked hazards: Clearly mark hazardous areas, such as slippery floors or areas with heavy machinery, to alert workers of potential dangers.
- Correct storage solutions: Design storage solutions that provide easy access, securely hold materials, and reduce the risk of falls or collapses.
By incorporating these design principles, warehouse managers can avoid common hazards and create a safer working environment for their employees. Prioritizing safety, employers can promote worker well-being, reduce the likelihood of accidents, and maintain productivity levels. Effective warehouse safety management involves training warehouse workers in safety procedures, developing comprehensive warehouse safety checklists, maximizing storage capacity while maintaining safety, implementing best practices for pallet racking, and ensuring the safe storage of hazardous materials. With vigilant safety management, warehouse operators can mitigate potential risks and create a culture of safety within the workplace.
Developing Comprehensive Warehouse Safety Checklists
Developing comprehensive warehouse safety checklists is an effective way to ensure that all safety protocols are followed consistently. Such checklists serve as a reminder for workers to prioritize safety and maintain workplace standards. Here are a few key areas that should be covered in warehouse safety checklists:
- Proper material handling: Guidelines for safe lifting techniques, equipment usage, and load capacity limits.
- Housekeeping and organization: Regular inspections to identify and address potential hazards such as spills, obstructions, or improperly stored items.
- Emergency preparedness: Procedures for handling emergencies, evacuation routes, location of safety equipment, and communication protocols.
- Equipment maintenance: Regular checks to ensure equipment is in good working condition, with proper training on equipment usage.
- Personal protective equipment (PPE) usage: Reminders for workers to wear the appropriate PPE for specific tasks.
- By developing comprehensive safety checklists, employers can reinforce safe practices, reduce the risk of accidents, and create a safety-conscious workplace culture.
Maximizing storage capacity is essential for efficient warehouse operations, but it must be done without compromising safety standards. Balancing storage capacity while maintaining safety requires careful planning and adherence to best practices. Here are some safety tips for maximizing storage capacity:
- Proper loading: Ensure items are loaded correctly, distributing weight evenly, and preventing overloading.
- Clearance space: Allow for adequate clearance space around storage racks, equipment, and walkways to prevent collisions and injuries.
- Proper shelving: Use appropriate shelving, such as pallet racking systems, to optimize vertical storage space without compromising safety.
- Safe stacking: Train workers on safe stacking techniques, ensuring stability and preventing the risk of items falling.
- Clear labeling: Clearly label items and storage areas for easy identification and retrieval, minimizing the risk of accidents.
- By following these safety tips, warehouse operators can maximize storage capacity while maintaining a safe work environment for employees.
Frequently Asked Questions
Some common hazards in a warehouse environment include falls from heights, forklift accidents, and slips and trips. Improperly stacked boxes or pallets can lead to falling objects that can cause serious injury. Exposure to hazardous materials, such as chemicals or dust, can also be a hazard in a warehouse environment. Regular safety training and inspections can help mitigate these hazards and ensure a safe working environment.
Companies can assess the safety of their warehouse and identify potential risks by conducting a thorough risk assessment. This assessment should include identifying hazards, such as slips, trips, and falls, and implementing safety protocols, including regular employee training and safety equipment requirements. Regular equipment and storage area inspections can also help ensure compliance with safety standards. Companies may consider hiring a third-party safety consultant to conduct an independent evaluation of their warehouse’s safety measures.
Some best practices for designing a safe and efficient warehouse layout include placing frequently picked items closest to the shipping area for faster processing, using clear signage and labeling to help workers navigate the warehouse, ensuring adequate walkway space for equipment and pedestrian traffic, and arranging inventory to maximize storage space without creating hazards or obstacles.
Recognizing the warning signs of a potentially unsafe warehouse environment is the first step toward improving safety standards. Some warning signs to watch out for include:
- Lack of proper body parts protection: Absence of hard hats, safety glasses, and safety shoes can indicate a lack of safety awareness.
- Ice buildup: Failure to address ice buildup can pose serious risks, especially in areas where machinery or workers operate.
- Noise levels: Excessive noise levels can signal the need for noise reduction measures, which are crucial for occupational health and safety.
- Long way to safety equipment: Workers’ safety can be compromised if safety equipment, such as fire extinguishers, is not easily accessible.
- Lack of safety standards: Inadequate safety standards for specific areas of the warehouse, such as loading docks or storage facilities, hint at potential safety hazards.
- By identifying these warning signs, warehouse operators can proactively address safety concerns, reduce the risk of accidents, and maintain a safe working environment for their employees.