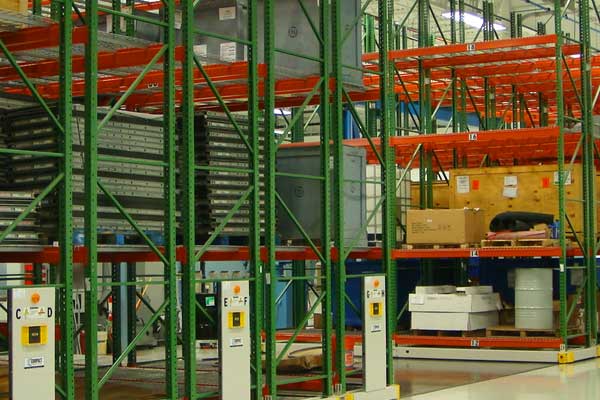
Maintenance of industrial storage systems is vital for smooth operations. Regular upkeep ensures longevity and functionality, reducing the risk of breakdowns. Implementing maintenance strategies like preventive and predictive maintenance can significantly impact the efficiency and cost-effectiveness of storage solutions. From inventory management to monitoring system health, proper maintenance enhances safety standards and optimizes storage space utilization. Understanding the importance of maintenance practices is crucial for businesses aiming to prevent costly downtime and maximize productivity.
Understanding Storage System Maintenance
Maintenance is the backbone of smooth industrial operations. In the realm of storage systems, it plays a pivotal role in upholding efficiency and longevity. By embracing preventive maintenance practices, businesses can avoid costly downtimes and equipment failures. Predictive maintenance takes this a step further by leveraging data analysis and sensors to anticipate issues before they arise. On the contrary, reactive maintenance, though necessary at times, is often more costly and can lead to operational disruptions. Understanding the nuances of maintenance strategies is vital for optimizing storage solutions and ensuring adherence to safety standards and specifications. Regular maintenance not only enhances equipment durability but also contributes to overall operational excellence. Employing the most effective ways of maintenance can have a significant impact on inventory management and warehouse productivity.
Definition and Importance
Regular maintenance for industrial storage systems encompasses a series of planned activities aimed at preventing equipment failure. This proactive approach involves various strategies such as preventive maintenance and predictive maintenance to ensure optimal system performance. The importance of regular maintenance cannot be overstated as it not only enhances the longevity of storage systems but also minimizes the risk of unexpected breakdowns. By adhering to maintenance schedules and conducting routine inspections, businesses can improve operational efficiency and reduce costly downtime. Investing in maintenance also aligns with safety standards and regulatory requirements, promoting a secure working environment for employees. Prioritizing maintenance practices indicates a commitment to maximizing the lifespan and functionality of storage systems, ultimately leading to increased productivity and cost savings.
Key Components of a Storage System
Storage systems consist of essential components crucial for efficient operations. Components like shelves, racks, bins, and containers provide the physical structure for item organization. Additionally, labeling systems play a vital role in quickly identifying stored items, enhancing retrieval speed. Safety equipment such as guards, barriers, and warning signs ensure a secure working environment, complying with industry standards. Equally important are inventory management systems for tracking stock levels and facilitating restocking. Implementing preventive maintenance schedules using predictive maintenance techniques helps in identifying potential issues before they escalate, ensuring optimal system performance. Monitoring tools like sensors and CMMS software further enhance the system’s reliability and longevity. Incorporating these key components ensures the smooth functioning of industrial storage systems.
Enhancing Efficiency through Regular Maintenance
Regular maintenance is crucial for enhancing efficiency in industrial storage systems. By performing preventive and predictive maintenance, businesses can reduce downtime and operational delays significantly. Proactive maintenance strategies not only optimize storage space utilization but also enhance overall system performance. Implementing software for maintenance scheduling and utilizing IoT for real-time monitoring further boost the efficiency of maintenance practices. By adhering to routine inspection checklists and training staff on maintenance protocols, companies ensure the longevity and reliability of their storage systems. These best practices not only minimize breakdowns but also contribute to improved productivity and cost savings in the long run. Efficient maintenance plays a vital role in keeping storage systems running smoothly and maximizing operational efficiency.
Reducing Downtime and Operational Delays
Efficient maintenance plays a crucial role in minimizing downtime and operational delays in industrial storage systems. By implementing preventive maintenance strategies and leveraging predictive maintenance techniques, businesses can proactively address potential issues before they escalate. Regular inspections, adherence to maintenance schedules, and the timely replacement of critical components can significantly reduce unexpected breakdowns. Moreover, the utilization of advanced technology such as sensors and CMMS facilitates real-time monitoring of system health, enabling quick response to any anomalies. By focusing on proactive maintenance practices, organizations can ensure uninterrupted operations, optimize productivity, and enhance overall efficiency, ultimately leading to cost savings and improved customer satisfaction.
Optimizing Storage Space Utilization
Proper utilization of storage space is essential for efficient operations in any industrial setup. By implementing smart storage solutions and regular maintenance practices, firms can maximize their warehouse capacity. Utilizing preventive maintenance strategies ensures that storage systems are always in optimal condition, reducing the risk of sudden breakdowns that can disrupt operations. This proactive approach not only minimizes downtime but also enhances the overall productivity of the facility. Incorporating data analysis and inventory management software can further streamline the process, allowing for real-time monitoring of available space and inventory levels. By optimizing storage space utilization through effective maintenance, companies can improve their bottom line and stay ahead in today’s competitive market.
Cost Savings and Budget Management
Understanding the financial implications of industrial maintenance is crucial. Regular maintenance practices such as preventive and predictive strategies can result in significant cost savings in the long run. By investing in maintenance upfront, businesses can avoid costly breakdowns and extend the lifespan of their machinery, ultimately reducing reactive maintenance expenses. Effective budget management involves optimizing inventory levels, monitoring consumables, and implementing data-driven analysis to streamline supply chain processes. Leveraging tools like CMMS and RCM can aid in tracking maintenance costs and ensuring efficient MRO inventory management. Prioritizing cost-effective solutions and adhering to best practices in maintenance can lead to improved budget allocation and overall financial health for the organization.
Preventive Maintenance vs. Reactive Repairs
Preventive maintenance involves scheduled inspections and proactive repairs to prevent equipment failures, while reactive repairs address issues only when they arise. Implementing preventive maintenance minimizes downtime, increases equipment longevity, and lowers repair costs compared to reactive approaches. By utilizing predictive maintenance strategies, businesses can predict when maintenance is needed based on data analysis and monitoring, further reducing unexpected breakdowns. In contrast, reactive repairs often result in unanticipated downtime, disrupting operations and impacting productivity. Investing in preventive maintenance not only ensures continuous system functionality but also enhances overall operational efficiency and cost-effectiveness in the long run. Combining preventive techniques with predictive insights can significantly optimize industrial storage system performance.
Long-term Financial Benefits of Regular Maintenance
Regular maintenance of industrial storage systems offers long-term financial benefits by reducing the risk of costly breakdowns and extending the lifespan of equipment. Implementing preventive maintenance strategies can help avoid unexpected expenses related to reactive maintenance. By conducting routine maintenance checks and utilizing predictive maintenance techniques, companies can identify potential issues before they escalate, leading to significant cost savings in the long run. Efficient maintenance practices also contribute to improved inventory management, ensuring optimal use of space and reducing the need for excess inventory. Investing in technology such as CMMS and IoT for monitoring and maintenance scheduling enhances operational efficiency, minimizes downtime, and ultimately results in cost-effective maintenance solutions.
Safety and Compliance
Ensuring safety and compliance within industrial storage systems is paramount. Industrial maintenance involving regular inspections and adherence to safety standards is crucial for mitigating risks. By implementing preventive maintenance strategies and utilizing safety equipment, companies can uphold safety regulations. Compliance with regulations not only safeguards employees but also prevents costly breakdowns. Proper inventory management of spare parts and consumables is essential to minimize downtime and optimize efficiency. Following best practices and conducting routine maintenance checks are the most effective ways to maintain safety and compliance in industrial storage systems. Embracing technological advancements such as IoT sensors and CMMS enhances monitoring capabilities, contributing to a culture of safety and compliance. Utilizing these methods guarantees a safe working environment and sustains the longevity of storage systems.
Ensuring Worker Safety
Regular maintenance of industrial storage systems is crucial for ensuring worker safety. By implementing preventive maintenance strategies, companies can minimize the risk of accidents and injuries in the workplace. Routine maintenance checks on safety equipment and adherence to safety standards are essential to create a secure working environment. Predictive maintenance techniques can help identify potential safety hazards before they escalate, contributing to a safer overall workspace. Monitoring system health through IoT technology can provide real-time data on equipment conditions, allowing for timely intervention to prevent breakdowns. Prioritizing worker safety through regular maintenance not only safeguards employees but also promotes a more efficient and productive operation in the long run.
Compliance with Industry Regulations
Regular maintenance of industrial storage systems is crucial for compliance with industry regulations. Adhering to specific maintenance schedules ensures that the systems meet safety standards and operate efficiently. By incorporating preventive and predictive maintenance strategies, businesses can proactively address issues, staying ahead of potential regulatory violations. Compliance also involves maintaining proper inventory management practices, ensuring that necessary spare parts and consumables are readily available. Following routine maintenance checklists and utilizing the most effective maintenance practices contribute to meeting regulatory specifications. Failure to comply can result in costly downtime, penalties, and reputational damage. Therefore, staying abreast of the latest maintenance technologies and industry standards is paramount.
Extending the Lifespan of Storage Systems
Regular maintenance is crucial for extending the lifespan of storage systems. By implementing preventive maintenance strategies, businesses can avoid costly breakdowns and increase the longevity of their industrial storage systems. Predictive maintenance, utilizing data analysis and sensors, can help in identifying potential issues before they escalate, thus significantly impacting the overall efficiency and productivity. Routinely inspecting and cleaning the storage systems, along with training staff on maintenance protocols, are among the best practices to ensure the longevity of the equipment. By investing in maintenance today, businesses can secure the reliability of their storage solutions and reduce the need for reactive maintenance in the long run.
Impact on Longevity and Performance
Regular maintenance significantly impacts the longevity and performance of industrial storage systems. By implementing preventive maintenance strategies, businesses can reduce the frequency of breakdowns and enhance system reliability. Predictive maintenance techniques, coupled with data analysis and monitoring using IoT sensors, play a vital role in identifying potential issues before they escalate, thus extending the lifespan of the equipment. This proactive approach not only ensures consistent performance but also minimizes the risk of unexpected downtime, leading to increased productivity and operational efficiency. Maintaining optimal performance through routine inspections and adherence to best practices in storage system maintenance is crucial for sustaining peak productivity and maximizing the lifespan of industrial storage systems.
Technological Advancements in Maintenance Practices
Utilizing software for maintenance scheduling has revolutionized industrial maintenance practices. This approach enables the proactive scheduling of tasks, moving away from reactive maintenance. IoT plays a pivotal role by continuously monitoring system health, detecting potential issues in real-time, and preventing unexpected breakdowns. By integrating these technologies, companies can streamline their maintenance strategies, leading to enhanced operational efficiency and cost savings in the long run. Implementing Computerized Maintenance Management Systems (CMMS) and Reliability-Centered Maintenance (RCM) methodologies further improves maintenance effectiveness. Embracing these innovations not only minimizes downtime but also ensures that storage systems operate at their optimal capacity, aligning with the most effective ways to manage industrial assets efficiently.
Using Software for Maintenance Scheduling
Implementing software for maintenance scheduling streamlines the process, aiding in preventive maintenance planning. This technology enables efficient scheduling of routine maintenance tasks based on equipment specifications and historical data analysis. By utilizing CMMS or RCM software, industrial facilities can enhance maintenance strategies and minimize downtime. The incorporation of predictive maintenance through software tools ensures timely identification of potential issues, contributing to cost savings in the long run. Moreover, these applications facilitate tracking MRO inventory, reducing lead times for spare parts procurement. Embracing software solutions for maintenance scheduling maximizes operational efficiency and optimizes inventory management, aligning with the best practices in industrial maintenance.
The Role of IoT in Monitoring System Health
IoT plays a pivotal role in monitoring the health of industrial storage systems by leveraging interconnected devices to gather real-time data on equipment performance. By using sensors and connectivity, IoT enables predictive maintenance, identifying issues before they escalate. This proactive approach minimizes downtime and reduces the likelihood of unexpected breakdowns. Moreover, IoT enhances operational efficiency by providing insights into usage patterns and system behavior, allowing for optimized maintenance scheduling. The continuous data analysis facilitated by IoT ensures that maintenance activities are timely and targeted, maximizing the longevity and reliability of storage systems. Leveraging IoT in monitoring system health is at the forefront of modern maintenance strategies, offering a significant advantage in maintaining a well-functioning storage infrastructure.
Best Practices in Storage System Maintenance
Routine inspection checklists are essential for ensuring the upkeep of industrial storage systems. By regularly inspecting key components such as shelves, racks, and safety equipment, potential issues can be identified and resolved promptly, reducing the risk of breakdowns. Training staff on proper maintenance protocols enhances the efficiency of maintenance tasks and promotes a culture of safety within the facility. Incorporating data analysis for inventory management and monitoring system health can significantly impact maintenance strategies. Implementing these best practices not only prolongs the lifespan of storage systems but also ensures smooth operations in the long run.
Routine Inspection Checklists
Effective routine inspection checklists are fundamental for maintaining industrial storage systems. These checklists outline specific tasks and areas to be inspected regularly, ensuring that potential issues are identified early on. By incorporating elements of preventive maintenance strategies, routine inspections help in detecting any signs of wear and tear before they escalate into major problems. This proactive approach enhances the overall longevity and performance of the storage systems, reducing the likelihood of unexpected breakdowns and costly repairs. Moreover, these checklists serve as a structured way to track maintenance activities and ensure compliance with safety standards and regulations, contributing to a safer work environment for employees.
Training Staff on Maintenance Protocols
Empowering staff with training on maintenance protocols is pivotal in ensuring the seamless operation of industrial storage systems. By imparting knowledge on preventive, predictive, and reactive maintenance strategies, employees can proactively address issues, minimizing downtime and operational delays. Training sessions also cover inventory management, safety standards, and the proper utilization of storage solutions. Educating staff on best practices and specifications equips them to handle maintenance tasks efficiently, ultimately leading to enhanced system longevity. With a well-trained workforce, companies can optimize maintenance practices, reduce the risk of breakdowns, and promote a culture of safety and operational excellence within their facilities.
Conclusion
Regular maintenance of industrial storage systems is essential for ensuring smooth operations and maximizing efficiency. By incorporating preventive and predictive maintenance strategies, businesses can significantly reduce downtime and operational delays. Implementing routine maintenance checks, utilizing advanced technologies like sensors and CMMS, and adhering to best practices in maintenance protocols are crucial for enhancing the longevity and performance of storage systems. Proper maintenance not only optimizes storage space utilization but also contributes to safety standards and cost savings in the long run. Incorporating maintenance strategies into supply chain management enhances inventory control and helps in identifying the most effective ways to manage spare parts and consumables. In conclusion, investing in regular maintenance is key to ensuring the seamless functioning of industrial storage systems, leading to improved productivity and overall operational success.