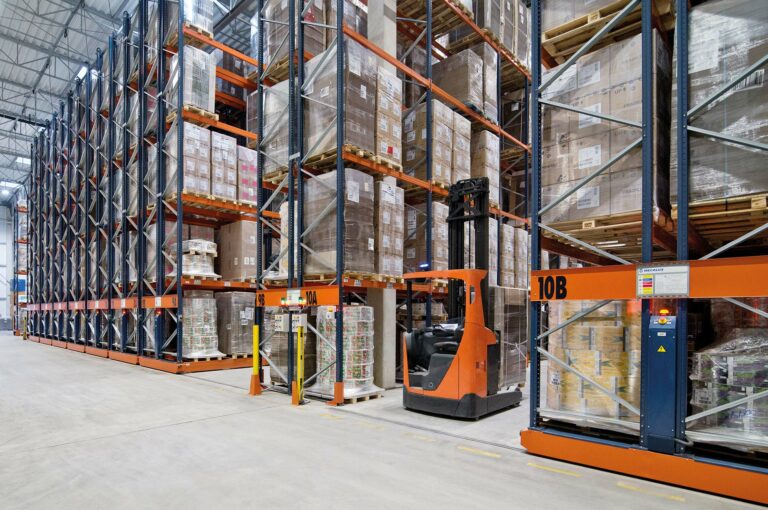
For warehouses, distribution centers, and manufacturing facilities, how space is managed can directly impact a business’s success. With limited space, increasing inventory, and the demand for fast, organized retrieval of products, businesses need reliable, scalable storage systems that adapt to their evolving needs. That’s where Bradford Systems’ Industrial Warehouse Racking Solutions come in.
Bradford Systems has established itself as a leader in industrial storage solutions by offering highly customizable, durable, and efficient racking systems designed to improve the overall efficiency of warehouse operations. Whether your warehouse requires selective racking for easy access to products, drive-in racking for dense storage, or cantilever racking for oversized items, Bradford Systems has the right solution to help you optimize your space and workflow.
In this blog, we’ll explore the various racking solutions offered by Bradford Systems, how they help industries achieve greater storage efficiency, and why industrial racking is an indispensable part of any warehouse management strategy.
Why Industrial Warehouse Racking is Essential
Storage challenges are common in industrial warehouses. As businesses scale, they need to manage larger inventories and optimize space without sacrificing access to goods. Without an efficient storage solution, cluttered spaces, disorganization, and bottlenecks in workflow can occur, leading to costly inefficiencies.
Industrial warehouse racking systems offer a structured and organized way to store goods, making it easy for businesses to maximize storage capacity, streamline workflows, and improve safety. Properly designed racking systems ensure that materials are stored in a way that allows for easy access, improved inventory management, and optimal use of vertical and horizontal space.
Here’s why investing in Bradford Systems’ racking solutions is essential for any warehouse or industrial facility:
- Maximized Storage Capacity: Racking systems allow businesses to use vertical space efficiently, meaning you can store more items without expanding your warehouse footprint.
- Improved Organization: With designated racking structures, goods can be organized based on size, type, or frequency of use, reducing retrieval time.
- Enhanced Safety: Properly designed racking systems ensure that heavy loads are stored securely, reducing the risk of accidents or product damage.
- Increased Efficiency: When items are stored efficiently, employees can find and retrieve goods faster, improving overall productivity.
Bradford Systems’ Industrial Warehouse Racking Solutions
Bradford Systems offers a wide range of racking solutions to meet the unique storage needs of various industries. From selective racking systems to high-density drive-in racks, Bradford Systems ensures that each solution is designed with durability, flexibility, and operational efficiency in mind.
Selective Racking Systems
Selective Racking is one of the most common and versatile racking systems used in warehouses. It is designed for direct access to each pallet, making it ideal for businesses with a wide variety of products that need to be easily accessible. Selective racking systems offer flexibility, as they can be configured to fit any warehouse size or shape.
Key Benefits:
- Direct access to every pallet, allowing for fast and easy retrieval of products.
- Adaptable layout that can be customized to fit different warehouse configurations.
- Cost-effective solution for warehouses with diverse inventory needs.
Selective racking is the ideal solution for warehouses that manage a wide range of SKUs and need fast access to all products. With selective racking, businesses can maintain high throughput while ensuring efficient storage of items.
Drive-In and Drive-Through Racking Systems
For warehouses that need to store large quantities of similar products or high-density inventory, Drive-In and Drive-Through Racking systems are an excellent option. These systems eliminate the need for multiple aisles by allowing forklifts to drive directly into the racking structure to access pallets. Drive-in racking operates on a Last In, First Out (LIFO) system, while drive-through racking works on a First In, First Out (FIFO) basis.
Key Benefits:
- Maximizes storage density by reducing the need for multiple aisles.
- Ideal for bulk storage of uniform products, such as seasonal goods or raw materials.
- Optimized space utilization, allowing for up to 75% more storage capacity compared to selective racking.
These systems are perfect for cold storage, bulk storage, or any warehouse that stores large quantities of the same product type. By eliminating unnecessary aisles, businesses can store more inventory in a smaller footprint, making it an efficient and cost-effective solution.
Cantilever Racking
Cantilever racking is specially designed for storing long, oversized, or bulky items such as lumber, pipes, or metal sheets. Unlike traditional pallet racking, cantilever racking uses horizontal arms to support products, allowing for easy loading and unloading of large materials.
Key Benefits:
- Ideal for storing long or irregularly shaped items, such as steel beams, pipes, and lumber.
- Open design allows for easy access and retrieval of materials.
- Can be configured in single- or double-sided arrangements, depending on warehouse needs.
Cantilever racking systems provide a flexible solution for industries such as construction, manufacturing, and metal fabrication, where storing long, heavy items is a common requirement. With its open, adjustable design, cantilever racking makes it easy to store and retrieve oversized items safely and efficiently.
Push Back Racking Systems
Push Back Racking is another high-density storage solution designed for warehouses that manage inventory on a LIFO basis. This system allows for multiple pallets to be stored on each level of a rack, with pallets “pushed back” as new ones are loaded. When a pallet is retrieved, the next pallet moves forward, making it easy to access inventory.
Key Benefits:
- Maximizes storage density by allowing pallets to be stored multiple levels deep.
- Ideal for warehouses with limited space but high inventory turnover.
- Reduces the number of aisles required, increasing overall storage capacity.
Push back racking systems are a great choice for businesses that need to store multiple pallets of the same product while optimizing space and improving retrieval times.
Pallet Flow Racking Systems
For warehouses that require a FIFO (First In, First Out) inventory system, Pallet Flow Racking offers the perfect solution. This system uses inclined rollers to allow pallets to move forward automatically as items are retrieved from the front. Pallet flow racking ensures that older stock is used first, making it ideal for perishable goods or products with expiration dates.
Key Benefits:
- FIFO inventory management ensures that the oldest products are used first.
- Continuous product rotation, perfect for perishable goods, such as food and beverages.
- High-density storage maximizes space while ensuring easy access to pallets.
This system is especially useful in industries like food and beverage, pharmaceuticals, and any business where managing product shelf life is critical.
Mobile Racking Systems
Mobile Racking is a highly efficient storage solution that allows for dynamic use of space. These systems are mounted on a track and can be moved to create temporary aisles, eliminating the need for permanent aisles between racks. By reducing the number of aisles, businesses can significantly increase storage capacity without expanding their warehouse footprint.
Key Benefits:
- Maximizes space utilization by eliminating the need for permanent aisles.
- Flexible layout, allowing aisles to be created only when needed.
- Ideal for small warehouses looking to double their storage capacity.
Mobile racking systems are ideal for high-density storage environments, such as cold storage or archival storage facilities, where maximizing available space is crucial.
Conclusion: Elevate Your Warehouse Efficiency with Bradford Systems
Bradford Systems’ industrial warehouse racking solutions provide businesses the tools they need to stay competitive in today’s fast-paced market. From maximizing storage space to improving inventory management and enhancing safety, our racking systems are designed to optimize every aspect of your warehouse operations.
Whether managing a large distribution center or a small warehouse, Bradford Systems offers customized solutions that align with your specific needs. Our team of experts works closely with you to design, install, and maintain a racking system that will transform how you manage your warehouse space.
For more information on how Bradford Systems can help you improve your warehouse efficiency, visit Bradford Systems Industrial Warehouse Racking.
What Is the Best Racking Solution for a Small Warehouse?
Selective pallet racking is usually the best option for small warehouses. This system uses wire decking or pallet supports on upright frames linked by row spacers. This design helps increase storage density and keeps everything easy to reach.
How Often Should Warehouse Racks Be Inspected?
Regular checking is very important for keeping your warehouse safe and ensuring your racking system can hold weight. You should visually check the pallet rack beams, connections, and teardrop pallet rack shelving at least once a month.