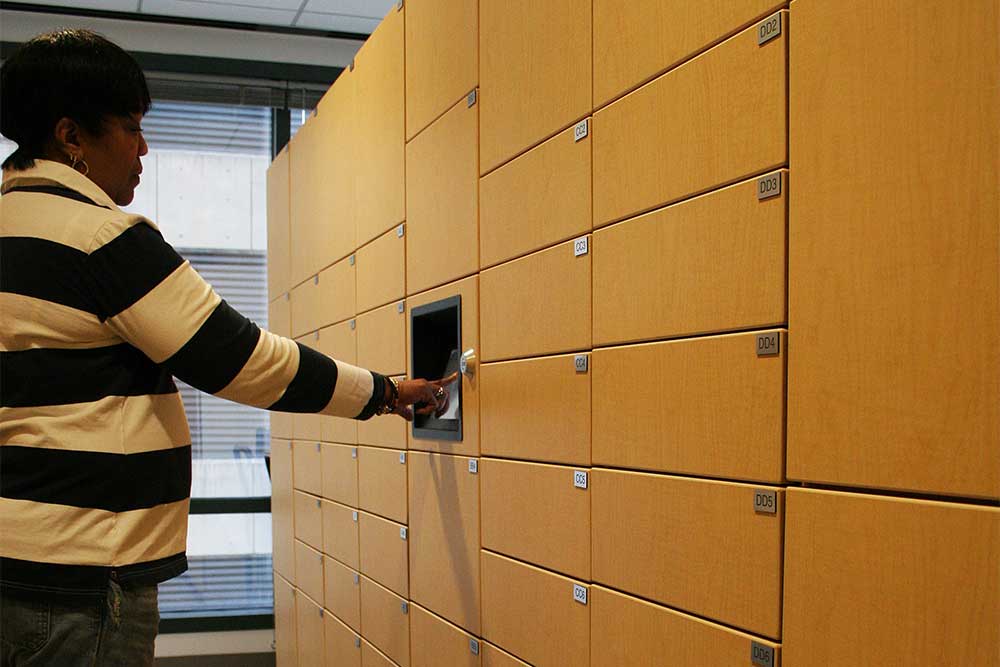
In today’s fast-paced manufacturing and logistics industries, every minute counts. Downtime, equipment losses, and tool mismanagement can lead to significant operational inefficiencies and increased costs. As these sectors strive for higher productivity and better asset management, advanced locker systems—especially smart lockers in manufacturing and employee lockers—are emerging as indispensable solutions. In this comprehensive blog, we explore how these cutting-edge storage systems enhance security for tools and equipment on the shop floor, reduce downtime, and prevent losses, all while boosting overall operational efficiency.
The Evolving Landscape of Manufacturing and Logistics
The Challenges on the Shop Floor
Manufacturing facilities and logistics centers encounter several challenges daily. Tracking thousands of tools and equipment is essential to prevent mismanagement. When tools go missing or are misplaced, production slows down, leading to unexpected costs.
Unauthorized access to sensitive equipment poses security risks. Theft, damage, or misuse can occur, especially in industries that require high precision and safety. These security breaches can cause production delays and create safety hazards.
Inadequate storage or misplaced tools lead to operational downtime, halting production lines. This directly affects productivity and results in lost revenue.
Efficient inventory management is crucial for tracking equipment. Poor inventory systems lead to overstocking or underutilization, impacting overall profitability. By addressing these challenges, facilities can enhance productivity and safeguard their assets.
Understanding Advanced Locker Systems
Smart lockers are technologically enhanced storage units equipped with digital access control, real-time monitoring, and data analytics. In the context of manufacturing, they are designed to store tools, equipment, and other high-value items safely while providing a seamless user experience on the shop floor.
Employee lockers serve a dual purpose. Not only do they provide personal storage for employees, but they can also be used to store work-specific items, ensuring that every tool has its designated place. These lockers are typically integrated into broader asset management systems to track and manage access effectively.
Key Features of Advanced Locker Systems
Digital access control in modern smart lockers uses key cards, biometric scanners, or mobile apps to ensure that only authorized personnel can access stored items. These systems also provide real-time monitoring and reporting through integrated sensors and software, allowing managers to track access events, usage patterns, and inventory levels. Instant alerts notify them of any discrepancies.
Administrators can customize access levels, assigning permissions based on roles or departments to safeguard sensitive or high-value tools. Built to endure harsh manufacturing environments, these lockers feature durable, industrial-grade materials that resist corrosion and physical damage.
Additionally, advanced locker systems seamlessly integrate with enterprise resource planning (ERP) and inventory management software, offering a unified view of asset usage and security.
Enhancing Security with Smart Lockers in Manufacturing
Smart lockers enhance security for tools and equipment in manufacturing environments. They control access by allowing only authorized employees to retrieve specific tools using digital credentials, biometric data, or PIN codes. This reduces the risk of theft and unauthorized use, which is crucial for high-value or specialized equipment.
These systems also provide detailed audit trails by logging every access event. If a tool is lost or damaged, managers can quickly identify who accessed it and when, promoting accountability and simplifying internal investigations.
Smart lockers help prevent tool misplacement by assigning designated storage compartments for each item, reducing the risk of tools being lost or left in the wrong place. Additionally, they enhance safety protocols by restricting access to hazardous tools, ensuring only trained personnel can use them, which minimizes the risk of workplace accidents.
Reducing Downtime
Downtime in manufacturing is costly, but advanced locker systems help minimize it by streamlining tool retrieval and inventory management. When tools are stored in designated smart lockers, employees can quickly locate and access them, reducing search time and preventing production delays.
Smart lockers also integrate with inventory management software to provide automated alerts for maintenance or low stock levels. This proactive monitoring prevents shortages and keeps the production line running smoothly.
By organizing storage and centralizing tool access, smart lockers optimize workflow. Employees spend less time navigating cluttered workspaces and more time on productive tasks, ultimately reducing idle time and increasing efficiency.
Preventing Losses and Enhancing Operational Efficiency
Loss prevention is essential in manufacturing, where replacing tools and equipment can be costly. Advanced locker systems significantly reduce tool loss by digitally tracking every item, ensuring nothing goes missing and preventing production delays. This leads to cost savings and uninterrupted workflow.
These systems also enhance asset management by providing detailed analytics on tool usage patterns. Managers can identify frequently used tools and underutilized equipment, allowing them to optimize inventory levels and reduce waste.
Storing tools in durable, industrial-grade lockers minimizes damage risk. Proper storage conditions protect equipment, extending its lifespan and reducing replacement costs.
The investment in smart locker systems quickly pays off through reduced losses, efficient inventory management, and minimized downtime, resulting in a higher return on investment (ROI) for manufacturers.
Strategic Benefits for Manufacturers
In today’s competitive market, manufacturers must optimize operations to stay ahead. Advanced locker systems provide strategic advantages by offering real-time monitoring for better decision-making, scalable designs that grow with operational needs, and enhanced compliance by restricting access to authorized personnel only. Additionally, adopting smart lockers showcases innovation, positioning manufacturers as industry leaders and strengthening their market reputation.
Conclusion
Advanced locker systems—including smart lockers in manufacturing and employee lockers—are revolutionizing the way manufacturers and logistics centers manage their tools, equipment, and operational workflows. By enhancing security, reducing downtime, and preventing losses, these innovative storage solutions offer a strategic advantage that directly translates to improved productivity and cost efficiency.
Are you ready to transform your manufacturing operations with a secure and efficient storage solution? Discover how Bradford Systems’ locker systems can help you enhance asset management and safeguard your shop floor. Contact Bradford Systems today to learn more about how our state-of-the-art smart lockers and employee lockers can elevate your operational efficiency and drive long-term success.
Can these locker systems be integrated with existing logistics infrastructure?
Absolutely. Locker systems are designed to integrate seamlessly with existing logistics infrastructure. Whether through API integrations or custom solutions tailored to your unique requirements, linking these systems with current warehousing software or applications is possible, often within a standard web browser.
How do advanced locker systems improve operational efficiency?
Operational efficiency gets a boost by streamlining package delivery and asset management. Workers can access or retrieve parcels or equipment swiftly using their mobile devices or ID cards. This eliminates wait times and allows for the quick location of any needed item via the smart locker solution.