Introduction: The Importance of Industrial Racks in Warehouses
In the fast-paced world of warehouse management, industrial racks for warehouses act as the backbone of operations. These essential storage solutions play a critical role in maintaining the flow of goods, optimizing space, and, ultimately, driving productivity. Often, corporate office managers grapple with the challenges of limited storage space, disorganized filing systems, and a lack of efficient storage organization. The right industrial racking system can address these pain points, transforming chaos into order while enhancing the overall efficiency of warehouse operations.
When it comes to warehouse racking, understanding the options available, abiding by safety requirements, and knowing how to maximize space are key. Whether you’re dealing with pallet racks, drive-in racks, or mobile sliding racks, each type of racking system has its specific advantages that can be leveraged to meet your unique storage needs.
In this comprehensive guide, we will explore the importance of industrial racks in warehouses, discuss the top options in the market, and delve into how Bradford Systems can provide you with tailored solutions to unleash the full potential of your storage space. So, if you’re ready to optimize your warehouse storage and improve organization, let’s dive in!
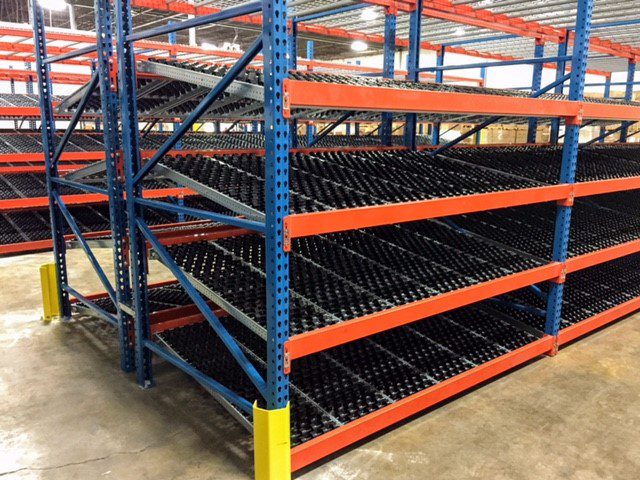
Understanding OSHA Requirements for Warehouse Racking
When it comes to warehouse storage, safety is paramount. The Occupational Safety and Health Administration (OSHA) sets out guidelines to ensure the safe storage of materials in warehouses. Understanding these requirements is the first step to choosing the right industrial racks for your warehouse.
Stacking and Stability Requirements
Keeping your warehouse safe starts with proper stacking. OSHA requires that items stored in tiers, be they bags, containers or bundles, need to be stacked, blocked, and interlocked in such a way that they achieve stability and security against sliding or collapse. This is where industrial racks come in handy. They provide a system that allows for secure stacking, with individual compartments for each item ensuring stability.
Moreover, certain types of industrial racks such as pallet racks, drive-in racks, or mobile sliding racks, are designed to interlock the stored items, providing an additional layer of safety. These racking systems also reduce the need for manual handling of goods, further minimizing the risk of accidents.
Height Limitations for Safety
Height restrictions are another key aspect of OSHA’s warehouse racking requirements. The guidelines mandate that stacked items should be limited in height to prevent them from becoming unstable and causing accidents.
While the specific height limitation can vary based on the type of items stored, the design of the racking system, and the specific conditions within the warehouse, most uprights in warehouse racking systems range in height from 8′ to 24′. This range ensures that items are stored at a height that is safe and practical for warehouse workers to access.
In conclusion, the OSHA requirements for warehouse racking are designed to enhance safety. As you consider which industrial racks to use in your warehouse, it’s important to choose those that not only meet your storage needs but also comply with OSHA’s guidelines for stacking stability and height limitations. In the next section, we’ll explore different types of industrial racks for warehouses to help you make an informed choice.
Different Types of Industrial Racks for Warehouses
Unlocking the potential of your warehouse space begins with understanding the different types of industrial racks available. Each type of racking system serves a unique purpose and is designed to cater to specific storage needs. Let’s take a closer look at four prevalent types of industrial racks for warehouses: selective racking, drive-in rack, carton flow rack, and mobile rack or mobile sliding rack.
Selective Racking
As the most common type of warehouse racking, selective racking offers the benefit of easy access to all pallets. This system allows for one pallet deep storage, enabling a large range of SKU’s to be stored. Selective racking is ideal for warehouses with a wide variety of products and high turnover rates.
Drive-In Rack
When seeking high-density storage, the drive-in rack system is a fitting choice. This system allows forklifts to drive directly into the rack to deposit or retrieve pallets. It’s particularly useful for storing large quantities of the same SKU. Drive-in racking is a popular choice for warehouses that handle bulk goods and operate on a Last In, First Out (LIFO) basis.
Carton Flow Rack
The carton flow rack system uses gravity to improve efficiency. It’s designed with a slight pitch, allowing cartons to flow from the loading end to the picking end. This system is a great choice for warehouses dealing with high-volume order picking with low SKU counts and is an essential component of an efficient First In, First Out (FIFO) product management system.
Mobile Rack or Mobile Sliding Rack
Mobile racks or mobile sliding racks are designed to maximize the use of warehouse space. These racks are mounted on guided mobile bases that slide along fixed tracks, eliminating the need for multiple fixed aisles. This type of racking system is an excellent choice for businesses looking to increase storage density while maintaining individual access to all pallets.
By understanding the unique features and benefits of each racking system, you can choose the most suitable industrial racks for your warehouse that align with your storage needs, workflow processes, and efficiency goals.
Standard Sizes of Warehouse Racks
In the world of industrial racks for warehouses, one size does not fit all. The dimensions of your warehouse racks can significantly impact your storage capacity, accessibility, and workflow efficiency. Therefore, it’s crucial to understand the standard sizes of warehouse racks to make an informed decision that best suits your storage needs.
Common Upright Depths
When it comes to the depth of uprights, or front-to-back measurements, the most common size found in industrial warehouses is 42 inches. However, depending on the size and nature of the items to be stored, 36- and 48-inch deep uprights are also standard sizes that cater to varying warehouse needs.
Variety of Heights
The height of warehouse racks offers a much more extensive range of options. Typically, uprights can range anywhere from 8 feet to 24 feet in height. The choice of height will depend on the vertical space available in your warehouse, the size of the goods to be stored, and your forklift reach capabilities. It’s essential to ensure that the height of your racks promotes easy accessibility while maximizing your warehouse’s vertical space.
Width of Uprights
Moving to the width, the measurement across the front face of the upright post, the vast majority of uprights are 3 inches wide. This standard width provides a balance between structural stability and space optimization, allowing enough space for the safe storage and retrieval of goods.
Understanding the standard sizes of warehouse racks can help you navigate the complexities of warehouse layout planning. It allows you to choose the right industrial racks for your warehouse, ensuring a balance between maximizing storage space, ensuring the safety of your employees, and maintaining efficient operations.
Bradford Systems: A Unique Approach to Warehouse Storage
Stepping into the world of industrial warehouse management, Bradford Systems offers a unique and holistic approach to warehouse storage solutions. Their expertise lies in designing and delivering storage systems that not only optimize space but also improve productivity and workflow. The company offers an array of products such as high-density shelving, smart lockers, day lockers, and other various industrial storage products.
High-Density Shelving
One of the key offerings from Bradford Systems is their High-Density Shelving. This shelving system is designed to maximize storage capacity by reducing unused aisle space. It’s a perfect solution for warehouses that need to store a large number of items in a limited space. The system is easy to use and can be configured to meet specific storage requirements, making it a versatile choice for various industries.
Smart Lockers
In an era where maximizing efficiency is a priority, Bradford Systems offers Smart Lockers. These lockers are designed with advanced technology that allows for secure storage and easy retrieval of items. They can be programmed to provide access only to authorized personnel, ensuring the safety of stored items. From employee lockers to package delivery lockers, Bradford Systems provides a smart solution for managing personal storage in a warehouse setting.
Day Lockers
For warehouses that operate on a shift basis, Day Lockers from Bradford Systems are an efficient solution. These lockers are designed for temporary storage, allowing employees to securely store their belongings during their work shift. They can be easily accessed and cleared out at the end of the day, ensuring effective usage and maintenance.
Industrial Storage Products
Beyond shelving and lockers, Bradford Systems offers a wide range of Industrial Storage Products. This includes vertical storage solutions, mobile racking systems, and heavy-duty mobile racking. These products are designed to handle heavy loads, provide easy access to stored items, and improve the overall organization within a warehouse.
By focusing on the unique storage challenges faced by warehouses, Bradford Systems provides innovative solutions that enhance efficiency and productivity. Their range of high-quality industrial racks and storage products are designed to cater to the diverse needs of warehouses, making them a top choice for warehouse managers looking to optimize their storage systems.
Enhancing Warehouse Efficiency with Industrial Racks
Industrial racks are not just about increasing storage area; they’re the secret weapon to an efficient warehouse. They play a critical role in optimizing storage space, controlling inventory, and ensuring safety. By choosing the right industrial racks, you can significantly enhance your warehouse’s overall efficiency.
Optimizing Storage Space
One of the key benefits of using industrial racks in your warehouse is their ability to optimize storage space. By installing tall storage racks or using mezzanine floors, you can significantly increase the amount of usable storage space in your warehouse. Moreover, standardized storage systems like pallet racking or shelving help maximize your storage capacity while maintaining efficiency and productivity. When all your storage systems are uniform, it becomes easier to organize and access your inventory, reducing the time needed to locate and retrieve items.
Controlling Inventory
Effective inventory management is a fundamental aspect of a well-functioning warehouse. By incorporating industrial racks into your warehouse, you can implement efficient inventory management practices such as the first-in, first-out (FIFO) method. This involves storing items in a way that allows for the oldest inventory to be accessed first, reducing the risk of spoilage or obsolescence.
Furthermore, industrial racks facilitate regular inventory audits and the implementation of a warehouse management system (WMS). A WMS can help you track inventory levels, manage order fulfillment, and optimize warehouse operations, all of which contribute to improved inventory control.
Ensuring Safety with Pallet Rack Safety Guards
Safety is a top priority in any warehouse, and industrial racks play a critical role in ensuring this. Pallet rack safety guards, for instance, are essential for preventing accidents caused by falling objects. They act as a barrier to stop items from falling off the racks, significantly reducing the risk of workplace injuries.
Moreover, OSHA requirements for warehouse racking mandate that items should be stacked, blocked, interlocked, and limited in height to ensure stability and prevent collapse. Compliance with these guidelines not only ensures safety but also increases the longevity and durability of your industrial racks.
In conclusion, industrial racks are more than just storage solutions. They’re instruments of efficiency, organization, and safety. By optimizing storage space, facilitating inventory control, and ensuring safety, industrial racks can significantly enhance your warehouse’s overall efficiency. As you consider your warehouse needs, look for a provider like Bradford Systems that offers a range of high-quality industrial racks designed to cater to your warehouse’s diverse needs.
Conclusion: The Role of Industrial Racks in Warehouse Management
Industrial racks play a pivotal role in warehouse management. They are the backbone of efficient inventory management, enabling businesses to maximize storage space, streamline operations, and boost productivity. But beyond mere utility, industrial racks contribute significantly to safety and organization within a warehouse, ensuring that operations run smoothly and efficiently.
Industrial racks, from selective racking to mobile racks, and their standard sizes provide a myriad of storage solutions. They cater to the unique needs of different businesses, accommodating various inventory types, sizes, and turnover rates. This versatility makes them an indispensable component in any warehouse setup.
Optimizing storage space is a crucial aspect of warehouse management, and industrial racks are instrumental to achieve this. By utilizing vertical space and organizing items effectively, these racks allow for a significant increase in storage capacity. This not only optimizes the use of available space but also enhances warehouse workflows and operational efficiency.
Equally important is the role of industrial racks in inventory control. Properly designed and implemented racking systems can support efficient inventory management practices, such as the first-in, first-out (FIFO) method, regular inventory audits, and the use of warehouse management systems. This, in turn, improves order fulfillment and reduces the risk of stock discrepancies.
Safety should never be compromised, and this is another area where industrial racks shine. By adhering to OSHA’s requirements for warehouse racking, including stability, height limitations, and aisle width, businesses can ensure a safe working environment. Moreover, accessories like pallet rack safety guards further enhance safety measures, preventing accidents and injuries.
As we’ve seen, Bradford Systems offers a unique approach to warehouse storage, offering high-density shelving, smart lockers, and a range of other industrial storage products. By providing versatile, high-quality solutions, they help businesses unleash space, streamline operations, and improve overall warehouse efficiency.
In conclusion, industrial racks for warehouses are more than just storage solutions—they are integral to the effective management of a warehouse. Whether you’re looking to maximize storage space, enhance inventory control, or ensure safety, investing in the right industrial racks is a crucial step towards achieving these goals. As you seek to optimize your warehouse operations, remember that the right racking systems can make a world of difference.