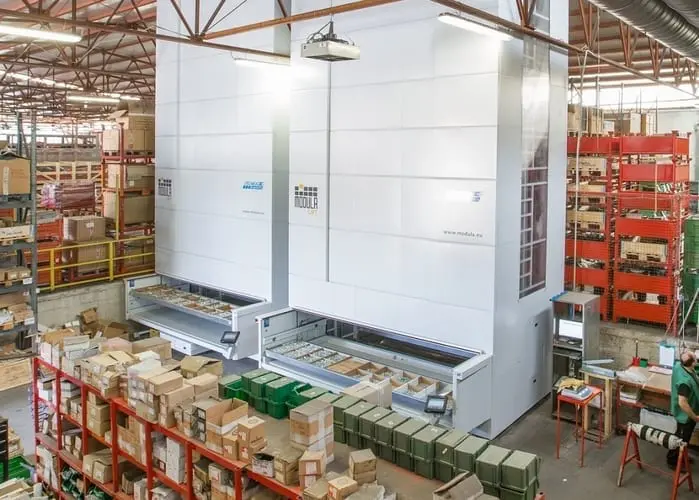
In the ever-evolving landscape of warehouse management, efficient storage solutions are essential for maximizing space, improving productivity, and ensuring smooth operations. As businesses expand and product volumes increase, traditional storage methods often fall short, leading to inefficiencies, cramped spaces, and increased operational costs. To address these challenges, innovative storage technologies like Vertical Lift Modules (VLMs) with columns of trays and Back Pallet Racking systems have emerged as powerful tools for optimizing warehouse environments and efficiently storing raw materials, including batch picking, for increased pick rates. One of the key benefits of VLMs is their ability to aid in order consolidation, allowing for more efficient and streamlined order fulfillment processes with a wide range of capabilities, specifications, and features.
In this blog, we will explore the benefits of these advanced storage solutions and delve into a case study involving Aurora Organic Dairy. The integration of Modula Vertical Lift Modules and Bulldog Push Back Racking significantly enhanced Aurora Organic Dairy’s storage capabilities and operational efficiency.
Vertical Lift Modules (VLMs): Revolutionizing Warehouse Storage
A smart library leverages advanced technology to offer an enriched, user-centric experience. This concept goes beyond just digitizing the library catalog; it encompasses many services that make library resources more accessible, efficient, and engaging. Smart libraries are designed to meet the demands of today’s tech-savvy patrons, providing seamless access to information, resources, and services through digital platforms, automated systems, and intelligent infrastructure.
Implementing smart lockers in libraries is a natural progression in developing smart libraries. These lockers provide a contact-free, automated solution for book pickup and drop-off, allowing patrons to access library services whenever needed. As libraries evolve into more flexible and versatile spaces, smart lockers, also known as smart locker systems, are becoming essential to the modern library ecosystem.
The Role of Library Pickup Lockers in Modern Libraries
Vertical Lift Modules (VLMs) represent the pinnacle of modern storage technology. Developed by Modula and proudly distributed by Bradford Systems, these automated storage systems are designed to maximize vertical space, streamline operations, and provide unparalleled efficiency in managing inventory.
Applications of VLMs
VLMs are versatile and can be applied across various industries, including manufacturing, pharmaceuticals, aerospace, and more. They are ideal for storing small to medium-sized items, spare parts, tools, and even temperature-sensitive products, as they can be customized to include cold or warm storage options.
Key Benefits of VLMs
Using a VLM system can bring many benefits that can change how warehouses operate. It does more than just provide more storage space; it also helps improve efficiency, accuracy, and safety.
Next, we will look closely at some of the main advantages of using VLMs.
Maximized Vertical Space Utilization
One of the most significant advantages of VLMs is their ability to utilize the full height of a warehouse. Traditional shelving and racking systems often leave valuable vertical space unused, but VLMs capitalize on this by stacking inventory vertically. This maximizes storage capacity and frees up floor space for other critical operations, resulting in a high ROI for businesses. Additionally, using a pallet-based VLM, entire pallets can be stored and retrieved, further maximizing vertical space utilization.
Automated Storage and Retrieval
VLMs are equipped with Automated Storage and Retrieval Systems (ASRS), also known as AS/RS, which automate placing and retrieving goods like full pallets from their storage locations. This warehouse automation reduces the need for manual labor, minimizes human error, and speeds up the picking process. One of the primary benefits of ASRS is its ability to store items in trays, automatically retrieved, and brought to the operator, streamlining warehouse processes and enhancing productivity through efficient product storage and retrieval with a wide variety of sizes, speed, cost, and flexibility. Additionally, ASRS technologies improve safety and ergonomics in the workplace, creating a more comfortable and efficient working environment for employees. By utilizing ASRS, operations can optimize their use of warehouse space and labor, making the most out of their vertical cube and ensuring efficient storage and retrieval of goods.
Improved Inventory Management
VLMs offer advanced inventory management capabilities, allowing real-time tracking of stored items. This ensures that inventory levels are always accurate, reducing the risk of stockouts or overstocking. The system’s software integration also allows seamless communication with existing warehouse management systems (WMS), providing a comprehensive overview of inventory status.
Space Savings
By utilizing vertical space and reducing the footprint of storage systems, VLMs can recover up to 90% of floor space. This is particularly beneficial for warehouses with limited space or businesses looking to expand their storage capacity without costly facility expansions.
Enhanced Security and Safety
VLMs provide secure storage for high-value items or sensitive materials. Access to stored items can be restricted to authorized personnel, and the system’s automated nature reduces the risk of accidents and injuries associated with manual handling of goods.
Push Back Pallet Racking: A High-Density Storage Solution
Push Back Pallet Racking is another innovative solution that addresses the need for high-density storage while maintaining easy access to stored items. This system is particularly well-suited for warehouses that deal with fast-moving inventory and require efficient use of space.
Applications of Push Back Pallet Racking
A pushback rack is ideal for industries that require efficient storage of palletized goods, such as food and beverage, retail, automotive, and manufacturing. It is particularly beneficial for managing inventory with a high turnover rate, where quick and easy access to goods is essential.
Key Benefits of Push Back Pallet Racking
Pushback pallet racking has many benefits. It is a popular option for many warehouses. This type of racking increases storage density. It also helps in organizing products better and boosts the overall productivity of the warehouse. In the following sections, we will examine these important benefits. This will show how pushback pallet racking can make warehouses work smoother and help you maximize your storage space.
High-Density Storage
Pushback rack allows for high-density storage by utilizing a single aisle for loading and unloading. Pallets are loaded onto inclined rails and pushed back to accommodate additional pallets behind them. This system can store multiple pallets deep, maximizing storage capacity without sacrificing accessibility.
Selective Accessibility
Unlike traditional racking systems, where accessing a pallet may require moving others, Push Back Racking allows for easy retrieval of pallets without disturbing the rest of the inventory. This selective accessibility is ideal for warehouses that manage a high volume of SKUs (Stock Keeping Units) with varying turnover rates.
Efficient Operation
Push Back Racking enables loading and unloading from the same aisle, reducing the time and effort required to manage inventory. This streamlined operation enhances efficiency and improves overall productivity in the warehouse.
Cost-Effective
Push Back Racking offers a budget-friendly solution for warehouses that need to maximize storage space without investing in expensive infrastructure. The system’s design also minimizes the need for additional forklifts or handling equipment, reducing operational costs.
Customizable and Scalable
Push Racking systems can be customized to meet specific storage requirements, including varying pallet sizes and weights. The system is also scalable, making it easy to expand or reconfigure as business needs evolve.
Case Study: Optimizing Storage for Aurora Organic Dairy with VLMs and Push Back Racking
Background
Aurora Organic Dairy (AOD) is a leading producer and processor of store-brand organic milk and butter for U.S. retailers. Based in Boulder, Colorado, AOD operates multiple dairy, heifer, and calf farms and processing plants in Colorado and Texas. In 2019, AOD embarked on an expansion project to build a new processing and storage facility in Columbia, Missouri, to extend its operations into the Midwest.
The new facility posed several challenges for AOD, including the need for refrigerated warehouse storage, pallet racking, and vertical storage that maximized their limited space. The facility’s long and narrow layout made traditional storage methods impractical, necessitating a customized solution for dry goods and temperature-sensitive products.
Challenges
Space Constraints:
The new facility’s long and narrow design presented a challenge in optimizing storage space. AOD needed a solution to maximize storage capacity without compromising accessibility or workflow efficiency.
Varied Storage Needs:
AOD required storage solutions for various products, including dry goods, milk samples, and maintenance parts. These products needed to be stored in cold and warm environments, adding another layer of complexity to the storage requirements.
Efficiency and Cost-Effectiveness:
As a rapidly growing company, AOD needed efficient and cost-effective storage solutions. The company sought to minimize operational costs while maximizing storage capacity and productivity.
Design Solution
To address these challenges, Bradford Systems worked closely with AOD to design a customized storage solution incorporating Modula Vertical Lift Modules (VLMs) and Bulldog Push Back Racking.
Push Back Racking for Pallet and Dry Good Storage:
- Initially, a high-density mobile pallet rack system was considered to optimize storage capacity. However, after evaluating the cost-effectiveness and operational requirements, it was decided that Push Back Racking would be a better fit for storing AOD’s fast-moving products.
- The Push Back Racking system was customized with specific beam levels to accommodate different pallet sizes, ensuring each product type had a designated storage space. The racking system was extended above the facility’s emergency exits, maximizing storage capacity without compromising safety.
- A high-density storage solution allowed AOD to manage their palletized goods efficiently, improving accessibility and operational flow.
Vertical Lift Modules for Parts Storage and Product Samples:
AOD implemented two Modula Vertical Lift Machines (VLMs) to store maintenance parts for their dairy processing equipment. The VLMs significantly reduced picking time by automating the storage and retrieval process, allowing AOD to maintain an organized inventory and quickly access critical parts when needed.
Additionally, two more VLMs were installed in the product sample testing area. These VLMs were customized to handle cold and warm storage requirements, with one unit designed for each temperature zone. To ensure optimal temperature control, the outer skins of the VLMs were left off above nine feet, allowing the HVAC system to circulate air effectively around the stored samples. The samples were accessed through a wall in the testing lab, providing a seamless and efficient workflow.
These VLMs provided the necessary storage for AOD’s product samples and incorporated the same ASRS benefits as the maintenance parts storage, further enhancing the facility’s efficiency and organization.
Results
Integrating Modula Vertical Lift Modules and Bulldog Push Back Racking provided Aurora Organic Dairy with a comprehensive storage solution that addressed their unique challenges. The VLMs maximized vertical space utilization, reduced picking times, and provided secure storage for sensitive products. At the same time, the Push Back Racking system offered high-density storage for palletized goods, improving accessibility and operational efficiency. The combination of these systems increased throughput, ensuring orders were fulfilled promptly and accurately while reducing floor space requirements and enhancing worker conditions. Adding a vertical carousel module, similar to a Ferris wheel, allowed for even more efficient storage and retrieval of products, further optimizing the warehouse storage system.
By choosing these advanced storage solutions, AOD was able to:
- Recover significant floor space: The VLMs allowed AOD to utilize vertical space, freeing up valuable floor area for other operations.
- Enhance operational efficiency: The VLMs’ automated storage and retrieval capabilities, combined with the Push Back Racking’s streamlined operation, significantly improved workflow efficiency.
- Achieve cost savings: The customized storage solutions were cost-effective, reducing the need for additional infrastructure and minimizing operational costs.
- Improve inventory management: The VLMs’ advanced inventory management features ensured accurate tracking of stored items, reducing the risk of stockouts or overstocking.
Conclusion
In conclusion, using vertical storage systems like VLMs and pushback pallet racking can greatly improve how you store items. These systems help you use space better, manage inventory well, and keep things safe. A case study of Aurora Organic Dairy shows how effective these solutions can be for businesses. By adding these new storage solutions, warehouses can store more items, work more efficiently, and save money. Welcoming these technologies can change your warehouse into a neat and organized place. This way, you ensure more efficiency and productivity.
How Does Pushback Pallet Racking Enhance Storage Density?
Pushback racking uses sloped rails and stackable carts to hold pallets up to 4-deep. It removes the need for regular access aisles. This setup helps to increase the unit load storage capacity in the same warehouse footprint.
How Do These Systems Integrate with Warehouse Management Software?
VLMs and pushback racking work well with WMS systems using software connections. This setup allows for real-time inventory tracking, better order picking, and smoother warehouse operations.