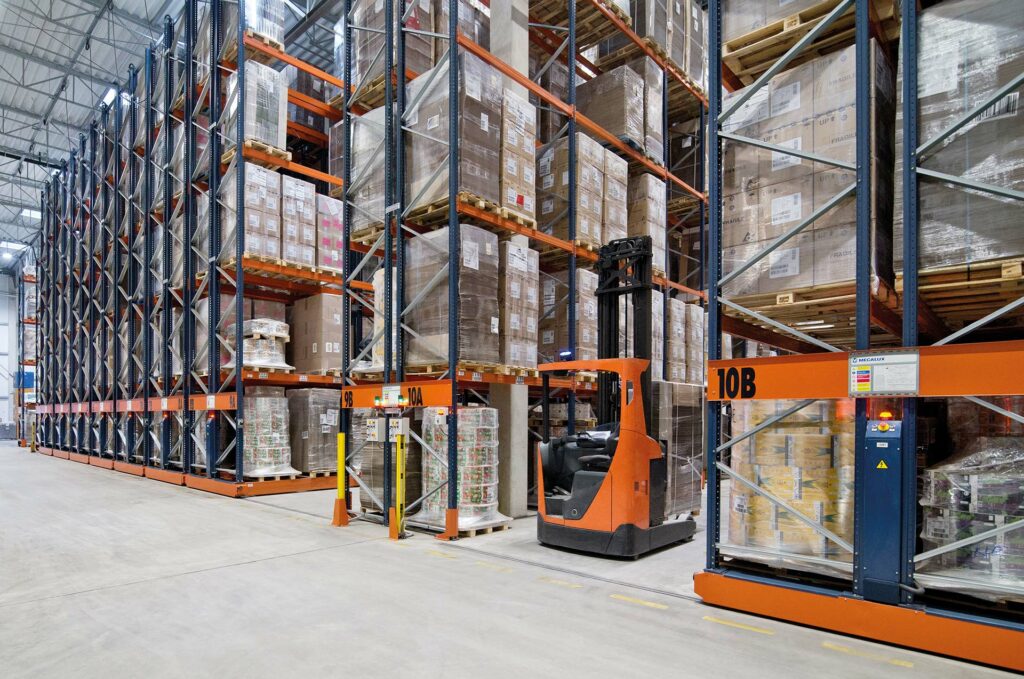
Efficient warehouse optimization is essential for businesses to streamline their operations, improve productivity, and maximize profitability. An optimized warehouse ensures smooth inventory management, effective space utilization, and streamlined labor processes. One key strategy for achieving warehouse optimization is implementing the First In, First Out (FIFO) method, which prioritizes the sale or use of older inventory items before newer ones. This method not only helps prevent obsolescence or spoilage but also contributes to accurate financial statements by accurately calculating the amount of inventory available.
In this blog, we will delve into the world of warehouse optimization strategies, with a focus on the FIFO method. We will explore its role in warehouse management and accounting, its benefits and disadvantages, and how businesses can effectively implement it in their warehouses. Additionally, we will discuss other key strategies for warehouse optimization, such as smart layout design, labor optimization, and inventory management techniques. By mastering these strategies, businesses can enhance their warehouse efficiency, improve customer satisfaction, and ultimately drive business success. To stay updated on the latest warehouse optimization strategies and tips, be sure to subscribe to our email newsletter.
The Pillars of Warehouse Efficiency
Efficient warehouse optimization relies on various pillars, including effective warehouse management, a well-optimized supply chain, and the implementation of proper inventory management methods. These pillars work together to ensure smooth operations, accurate inventory tracking, and timely order fulfillment. By following proven best practices in these areas, businesses can achieve optimal warehouse efficiency and enhance their overall operational performance.
- Implementing Smart Layout Design for Optimal Space Utilization. A well-designed layout ensures efficient movement of inventory, minimizes travel distance for workers, and optimizes storage capacity. By organizing the warehouse layout based on product demand, proximity to shipping areas, and efficient picking routes, businesses can streamline their operations, reduce labor costs, and improve overall warehouse efficiency. Utilizing technologies like warehouse layout optimization software can help in designing an optimal layout that considers various factors such as product dimensions, storage requirements, and operational workflows.
- Enhancing Labor Productivity through Effective Labor Optimization Strategies. By implementing strategies such as cross-training, labor scheduling optimization, and performance tracking systems, businesses can improve workforce efficiency, reduce labor costs, and enhance overall productivity. These strategies involve analyzing labor requirements, assigning tasks based on employee skills, and implementing performance-based incentives. Additionally, leveraging technology solutions like labor management software can help in automating labor-related processes, tracking employee performance, and optimizing workforce allocation. By streamlining labor operations, businesses can not only see cost savings but also reduce associated costs such as climate control, lighting, maintenance, and labor costs.
Inventory Management Techniques for Modern Warehouses
Efficient inventory management is crucial for modern warehouses to ensure accurate inventory tracking, minimize stockouts, and optimize order fulfillment processes. Implementing inventory management techniques such as the FIFO method, the most widely used method of valuing inventory globally, which aligns the expected cost flow with the actual flow of goods, utilizing inventory management software, and integrating an efficient inventory system can greatly improve inventory visibility, reduce carrying costs, and enhance overall warehouse efficiency. By adopting these techniques, businesses can better manage their inventory levels, improve order accuracy, and meet customer demands effectively.
Advantages of FIFO (First In, First Out) in Inventory Management
The FIFO method offers several advantages when it comes to inventory management. It ensures that older inventory is utilized before newer inventory, resulting in various benefits for businesses. Some advantages of the FIFO method include:
- Prevents obsolescence and spoilage: By prioritizing the sale or use of older inventory, the FIFO method helps prevent obsolescence or spoilage of goods.
- Accurate inventory valuation: FIFO contributes to accurate inventory valuation, as it reflects the actual cost of goods sold more accurately, especially when the cost of goods tends to increase over time.
- Cost-effective inventory management: FIFO reduces the risk of carrying excess inventory, minimizing carrying costs and optimizing cash flow.
- Mitigates inventory holding costs: By utilizing older inventory first, the FIFO method helps reduce inventory holding costs, such as storage and insurance expenses.
- Enhances financial reporting: The FIFO method contributes to more accurate financial statements, providing a clearer picture of a company’s financial performance and profitability.
Implementing the FIFO method can lead to improved inventory management, reduced inventory costs, and better financial decision-making for businesses.
Employing Accurate Forecasting Tools for Demand Prediction
Accurate demand prediction is vital for efficient warehouse optimization. By employing advanced forecasting tools and leveraging data analytics, businesses can better anticipate customer demand, optimize inventory levels, and reduce stockouts or overstocking. These forecasting tools use historical sales data, market trends, and predictive algorithms to generate accurate demand forecasts. By integrating these forecasts into inventory management systems, businesses can proactively plan their inventory, optimize order fulfillment processes, and align their supply chain operations to meet customer demands effectively. Accurate demand prediction through forecasting tools not only improves warehouse efficiency but also enhances customer satisfaction by ensuring products are available when and where customers need them.
Advanced Solutions for Warehouse Optimization
In addition to the aforementioned strategies, advanced solutions such as automation technologies play a significant role in warehouse optimization. Automation solutions, including robotics, automated storage and retrieval systems (AS/RS), and conveyor systems, can streamline warehouse operations, improve productivity, and enhance overall efficiency. These technologies automate repetitive tasks, reduce the risk of human error, and enable faster order fulfillment. By integrating automation solutions into warehouse operations, businesses can optimize their processes, minimize labor costs, and improve overall warehouse efficiency.
- Integrating Automation Solutions to Streamline Operations can significantly streamline processes and improve overall efficiency. Automation technologies such as robotics and AS/RS automate tasks such as picking, packing, and sorting, reducing manual labor and enabling faster order fulfillment. These technologies can be seamlessly integrated with existing warehouse management systems (WMS) to optimize operations, improve inventory accuracy, and reduce turnaround time. By automating repetitive tasks, businesses can minimize errors, increase productivity, and achieve higher levels of operational efficiency. Furthermore, automation solutions enable real-time tracking and monitoring of inventory, allowing businesses to make data-driven decisions, optimize space utilization, and enhance overall warehouse performance.
- Utilizing Cross-Docking Techniques for Efficiency that involves transferring goods directly from inbound shipments to outbound shipments, bypassing the need for long-term storage in the warehouse. This technique improves supply chain efficiency by reducing handling and storage time, enabling faster order fulfillment and reduced inventory holding costs. By implementing cross-docking techniques, businesses can optimize their supply chain operations, minimize order processing time, and improve overall warehouse efficiency. This strategy is particularly beneficial for industries with fast-moving products or perishable goods, where reducing turnaround time is crucial. Cross-docking can be facilitated through advanced logistics management systems, real-time tracking, and efficient coordination between suppliers, warehouses, and transportation providers.
Ensuring Inventory Accuracy and Compliance
Maintaining accurate inventory records and compliance with safety regulations is essential for warehouse optimization. Regular audits on inventory ensure accurate tracking, reduce inventory discrepancies, and enable timely identification of potential issues. Compliance with safety regulations ensures a safe working environment, minimizes the risk of accidents, and avoids penalties or legal consequences. By conducting regular audits, implementing inventory control measures, and adhering to safety regulations, businesses can ensure inventory accuracy, streamline processes, and maintain a compliant and safe warehouse environment.
Regular Audits on Inventory for Precise Tracking
Regular audits on inventory play a crucial role in ensuring precise tracking and maintaining inventory accuracy. These audits involve comparing physical inventory counts with recorded inventory levels, identifying discrepancies, and taking corrective measures. By conducting regular audits, businesses can minimize inventory discrepancies, reduce stockouts or overstocking, and improve overall warehouse efficiency. A text table can be used to provide a detailed breakdown of the auditing process, including key steps, frequency, and documentation requirements, all of which can be found on the company’s balance sheet.
Column Name A | Column Name B |
Audit Process | Conduct physical inventory counts and compare with recorded inventory levels |
Frequency | Regularly, ideally on a monthly or quarterly basis |
Documentation | Maintain records of inventory counts, discrepancies, and corrective actions taken |
By implementing regular audits on inventory, businesses can ensure precise tracking, identify potential issues, and maintain accurate inventory records.
Adhering to Safety Regulations and Standards
Adhering to safety regulations and standards is crucial for maintaining a safe working environment and ensuring compliance with legal requirements. By implementing safety protocols, conducting regular safety inspections, and providing proper training to employees, businesses can reduce the risk of accidents and promote a culture of safety in the warehouse. Compliance with safety regulations not only protects employees from potential hazards but also helps in avoiding penalties or legal consequences. Warehouse managers should stay updated with safety regulations specific to their industry and ensure their warehouse operations meet the necessary standards. By prioritizing safety and compliance, businesses can create a safe working environment, minimize the risk of accidents, and optimize overall warehouse efficiency.
Frequently Asked Questions
The FIFO method can transform warehouse operations by ensuring efficient inventory management, accurate inventory valuation, and improved financial statements. By prioritizing the sale or use of older inventory, businesses can prevent obsolescence, reduce inventory holding costs, and optimize overall warehouse efficiency.
Automating warehouse processes offers several key benefits, including increased efficiency, improved productivity, cost savings, and enhanced accuracy. By leveraging automation technologies, businesses can streamline operations, minimize manual labor, and optimize overall warehouse performance.
Space utilization plays a crucial role in overall warehouse efficiency. Optimizing space through smart layout design, proper storage systems, and efficient utilization of available space can enhance operational workflows, reduce travel time, and improve overall warehouse efficiency.
Yes, forecasting tools can significantly reduce inventory costs by enabling accurate demand prediction, optimizing inventory levels, and minimizing stockouts or overstocking. By leveraging data analytics and advanced forecasting models, businesses can optimize their inventory, reduce carrying costs, and achieve cost savings.
Strategies for labor optimization in warehousing include cross-training employees, optimizing labor schedules, implementing performance tracking systems, and leveraging technology solutions. These strategies enhance workforce productivity, reduce labor costs, and improve overall operational efficiency.
Inventory audits should be conducted regularly to ensure accuracy and compliance. Ideally, audits should be performed on a monthly or quarterly basis, depending on the volume of inventory and the specific requirements of the business.
Cross-docking is important for modern warehousing as it enables faster order fulfillment, reduces handling and storage time, and improves overall supply chain efficiency. By bypassing long-term storage, cross-docking optimizes operational workflows and enhances overall warehouse efficiency.